Now more than ever, with the current cost of living crisis escalating, companies are looking to increase their profitability whilst ensuring their processes are efficient and cost-effective.
We are here to show you the three most effective cost-saving solutions you can add to your Natgraph Machine as a retrofit to upgrade your savings whilst saving energy and becoming a more sustainable business.
#1 Heat Exchanger
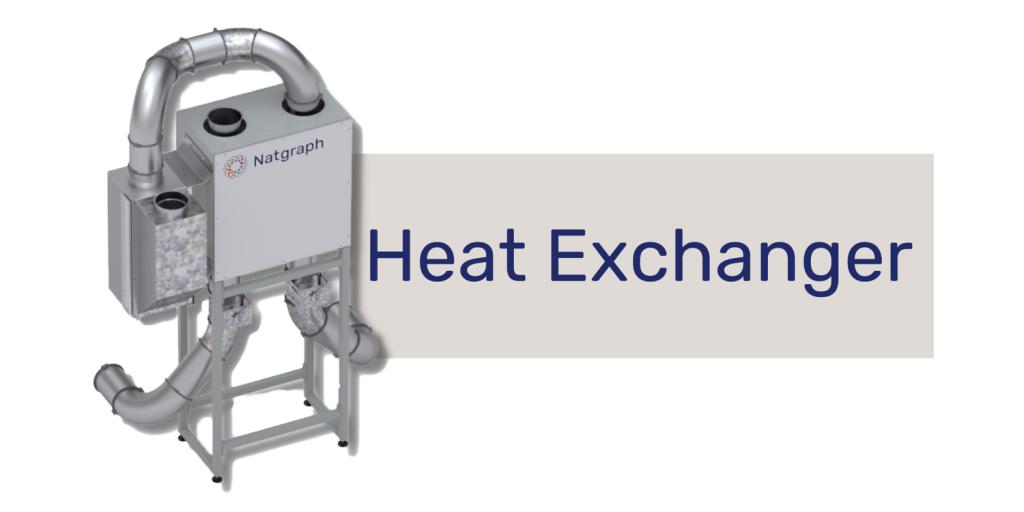
Heat Exchangers help to increase your efficiency and save money on running costs by preheating the intake air from the exhaust air which minimises the energy required to bring the cool air up to temperature.
#2 IECS
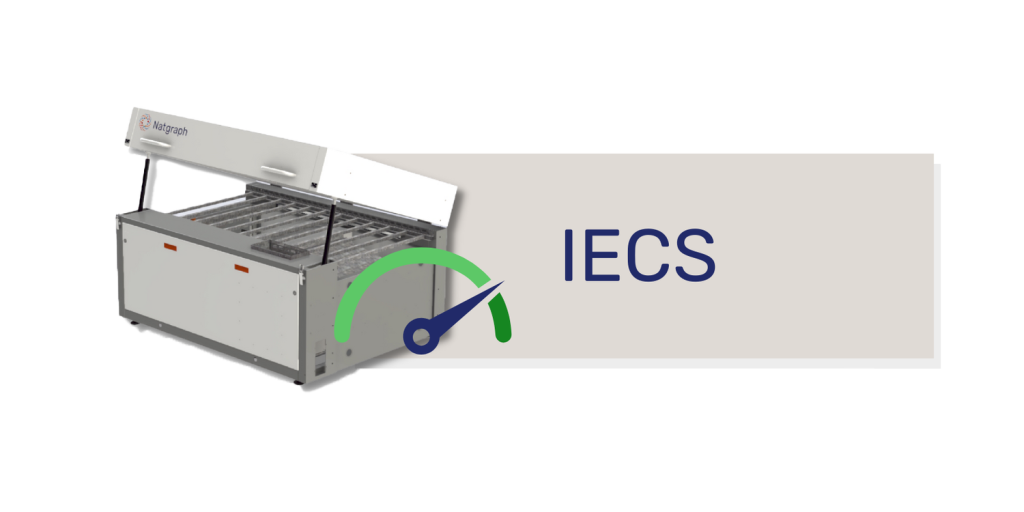
The Intelligent Energy Control System (IECS) aligns dryer energy consumption with process activity.
If the press is in a standby condition, the dryer will enter low power mode. The dryer awaits a signal and then instantly recommences at the previous settings with no additional power-up time.
Generally, this retrofit option will pay for itself in savings in less than a year!
Want to see the figures for yourself? Give us a call and we’ll be happy to show you.
#3 Ozone Filters
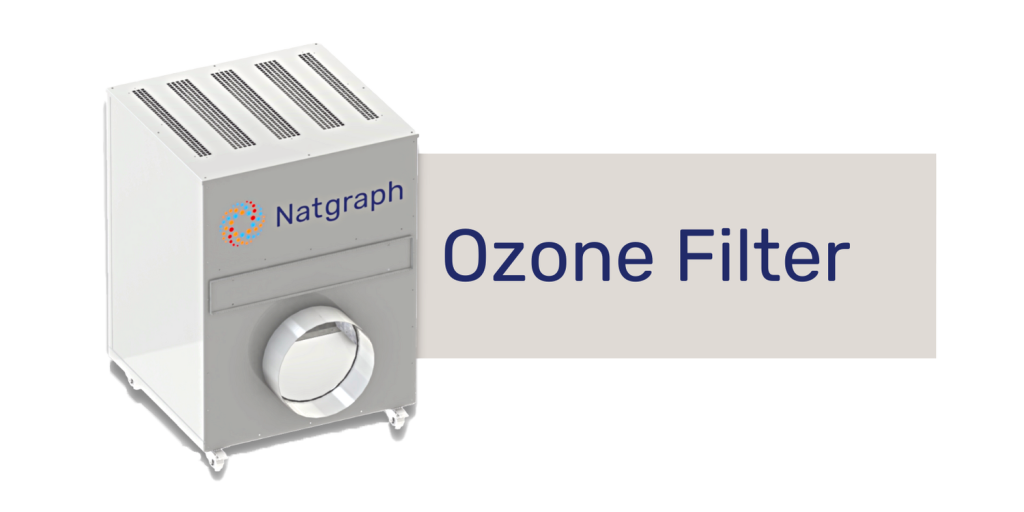
The Ozone Filter uses a replaceable charcoal filter and pre-filter to remove ozone gases produced by the UV curing process from the exhausted waste air.
The clean warm exhaust air can then be used to heat your factory, this is especially useful in colder months.
Find Out More
Want to learn more about our wider product offering? Click on the button below to request a copy of our complete product information brochure.